In the manufacturing industry, precise temperature monitoring is essential to ensure product quality, safety, and efficiency. Wireless RTDs (Resistance Temperature Detectors) have emerged as a reliable, cost-effective solution for temperature monitoring in a variety of applications. By offering real-time insights and eliminating the need for complex wiring, wireless RTDs by Swift Sensors enable seamless integration into diverse manufacturing environments. This article explores how wireless RTDs can revolutionize temperature monitoring in boiler rooms, food processing facilities, paint booths, and refrigeration rooms.
What Are Wireless RTDs?
Wireless RTDs use resistance changes in their sensing element to measure temperature accurately. These devices are designed to transmit temperature data wirelessly to a central monitoring system, enabling remote tracking and real-time alerts. The wireless capability reduces installation costs, simplifies maintenance, and increases flexibility, making them ideal for various manufacturing settings.
Applications of Wireless RTDs in Manufacturing
1. Boiler Rooms: Ensuring Process Continuity and Safety
Boiler rooms play a critical role in manufacturing by supplying hot water or thermal oil for processes such as cooking, cleaning, and heating. However, unmonitored temperature variations can lead to inefficiencies, equipment failures, or unsafe conditions.
- Solution: Wireless RTDs can be deployed in boiler rooms to continuously monitor water or thermal oil temperatures. By providing real-time data, these sensors help ensure the system operates within optimal temperature ranges, preventing overheating or underperformance.
- Benefits:
- Improved operational safety.
- Prolonged boiler and equipment lifespan.
- Enhanced energy efficiency, reducing fuel consumption and costs.
2. Food Processing: Maintaining Product Safety and Compliance
In the food manufacturing sector, precise temperature control is vital to comply with stringent safety regulations and ensure product quality. Cooking, chilling, and storing food at incorrect temperatures can lead to contamination or spoilage.
- Solution: Wireless RTDs can monitor temperatures at various stages of food production, from ovens and chillers to walk-in refrigerators. They provide real-time data that helps maintain proper cooking and storage conditions.
- Benefits:
- Enhanced compliance with food safety standards (e.g., HACCP).
- Reduction in food waste.
- Improved quality control during production and storage.
3. Paint Booths in Automotive Manufacturing: Precision for Quality Finishes
In automotive manufacturing, paint booths require strict temperature control to ensure that paint adheres uniformly to vehicle surfaces. Variations in temperature can result in uneven finishes, increased rework, and higher costs.
- Solution: Wireless RTDs can be installed inside paint booths to provide continuous temperature monitoring, ensuring that environmental conditions meet the exact specifications for paint application and curing.
- Benefits:
- Improved finish quality.
- Reduction in rework and waste.
- Increased production efficiency.
4. Refrigeration Rooms and Walk-Ins: Protecting Perishables
Refrigeration is critical in food manufacturing and storage. Even minor temperature deviations in refrigeration rooms or walk-ins can compromise product quality and safety, leading to significant losses.
- Solution: Wireless RTDs can be used to monitor refrigeration temperatures, alerting managers to any deviations from the desired range. This proactive approach helps prevent spoilage and ensures compliance with food storage regulations.
- Benefits:
- Real-time alerts for temperature deviations.
- Compliance with regulatory standards.
- Prolonged shelf life of products.
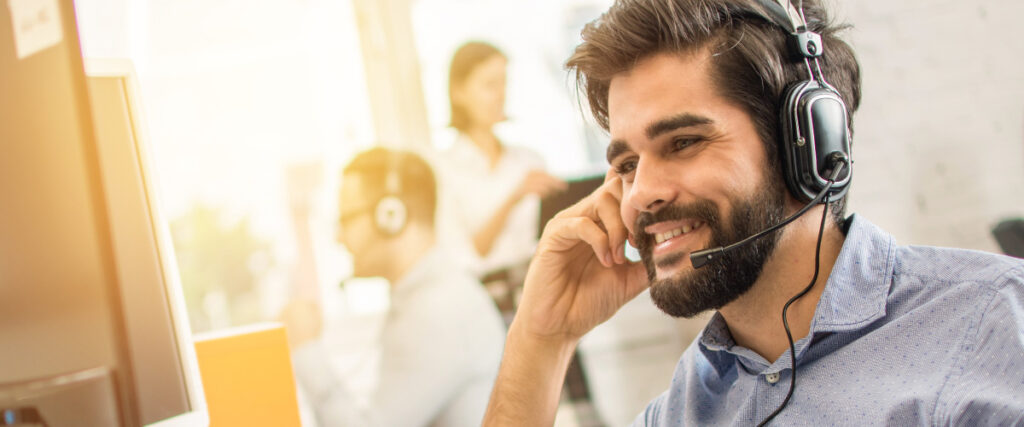
Talk with a Specialist
If you think it can’t be monitored, contact us, we might surprise you.
How Swift Sensors Can Help
Advantages of Wireless RTDs for Manufacturing
- Ease of Installation: Wireless RTDs eliminate the need for extensive wiring, reducing installation time and cost.
- Scalability: Additional sensors can be easily integrated as manufacturing needs evolve.
- Real-Time Monitoring: Continuous data transmission enables immediate corrective actions, minimizing downtime and preventing product loss.
- Data Insights: Historical data can be analyzed to optimize processes and identify trends.
- Flexibility: Wireless sensors can be placed in hard-to-reach or hazardous areas, enhancing overall monitoring capabilities.
Conclusion
Wireless RTDs are transforming temperature monitoring in manufacturing, offering unparalleled precision, convenience, and reliability. Whether managing boiler rooms, ensuring food safety, maintaining perfect paint finishes, or safeguarding refrigerated products, these advanced sensors are a must-have for modern manufacturing operations. By integrating wireless RTDs into their processes, manufacturers can not only ensure product quality and regulatory compliance but also achieve significant cost savings and operational efficiency.
For more information on how wireless RTDs can enhance your manufacturing processes, contact Swift Sensors. We specialize in wireless sensor solutions that help industries stay ahead in a competitive landscape.
Stay in the Know with Swift Sensors
Sign up for the Swift Sensors newsletter to stay ahead in sensor technology. Get exclusive updates on industry trends, product releases, and special promotions. Elevate your knowledge and be part of our tech community. Signup now!