Introduction
In the fast-paced world of industrial manufacturing, efficiency and innovation are not just goals, but necessities for survival and growth. A key player in this evolving landscape is the adoption of cutting-edge technologies like wireless power monitoring sensors. Swift Sensors, as a pioneering force in this arena, is enabling industries to redefine their operational efficiency and environmental footprint. This article delves into the reasons behind the growing adoption of wireless power monitoring sensors in industrial manufacturing, highlighting how they are revolutionizing traditional practices.
1. Enhanced Efficiency and Productivity
Efficiency is the cornerstone of any successful manufacturing operation. Wireless power monitoring sensors are changing the game by providing precise, real-time data on energy consumption. This data is instrumental in identifying inefficiencies, be it in machinery performance, operational timings, or process flow. Unlike traditional systems that rely on periodic manual checks and are prone to errors, these sensors offer continuous monitoring, ensuring that no energy wastage goes unnoticed.
The ease of installation of wireless sensors is another critical factor. Unlike wired systems that require extensive and disruptive installation processes, wireless sensors can be placed strategically across facilities without the need for extensive cabling. This not only reduces installation time but also offers flexibility in sensor placement, crucial for comprehensive energy monitoring. For instance, sensors can be easily deployed in hard-to-reach areas, providing a more complete picture of energy usage.
Wireless systems facilitate quicker reconfiguration and scaling. As manufacturing processes evolve, sensors can be easily moved or added, ensuring that the monitoring system always aligns with current operational needs. This adaptability is essential in an industry where change is constant, and staying ahead means being able to quickly respond to new challenges and opportunities.
2. Cost Reduction
Cost management is a vital consideration for any manufacturing unit, and wireless power monitoring sensors contribute significantly in this aspect. By identifying areas of excessive energy use, these sensors enable manufacturers to implement targeted measures to reduce consumption, leading to direct savings on energy bills.
In addition to direct energy savings, the lower installation and maintenance costs of wireless sensors compared to wired systems translate to substantial cost reductions. Wired systems often require extensive infrastructure changes, regular maintenance, and can be expensive to modify or scale. Wireless sensors, on the other hand, have minimal installation requirements and are easier to maintain, thanks to their lack of physical connections that can wear out or become damaged.
The data provided by these sensors can lead to long-term cost savings. By analyzing energy consumption patterns, manufacturers can optimize their processes, schedule high-energy tasks during off-peak hours, and make informed decisions about machinery upgrades or replacements. This strategic approach to energy management not only reduces immediate costs but also contributes to sustained financial health by optimizing asset utilization and extending equipment life.
3. Supporting Sustainable Practices
Sustainability is increasingly becoming a critical factor in industrial operations, driven by both regulatory requirements and a growing societal emphasis on environmental responsibility. Wireless power monitoring sensors are pivotal in this context, as they enable industries to minimize their environmental impact by optimizing energy use.
By providing detailed insights into energy consumption, these sensors help manufacturers identify and implement more energy-efficient practices. This not only reduces the environmental impact of their operations but also aligns them with global sustainability goals and regulations, an important factor in maintaining a positive public image and market competitiveness.
Additionally, the ability to monitor energy usage in real-time allows for immediate corrective actions, reducing waste and promoting a culture of sustainability within the organization. This proactive approach to environmental stewardship is essential in an era where businesses are expected to be at the forefront of ecological conservation efforts.
The data gathered by these sensors can be used to support sustainability reporting and compliance with environmental standards. By providing accurate and detailed energy usage data, manufacturers can more effectively report on their sustainability initiatives and progress, further reinforcing their commitment to environmentally responsible practices.
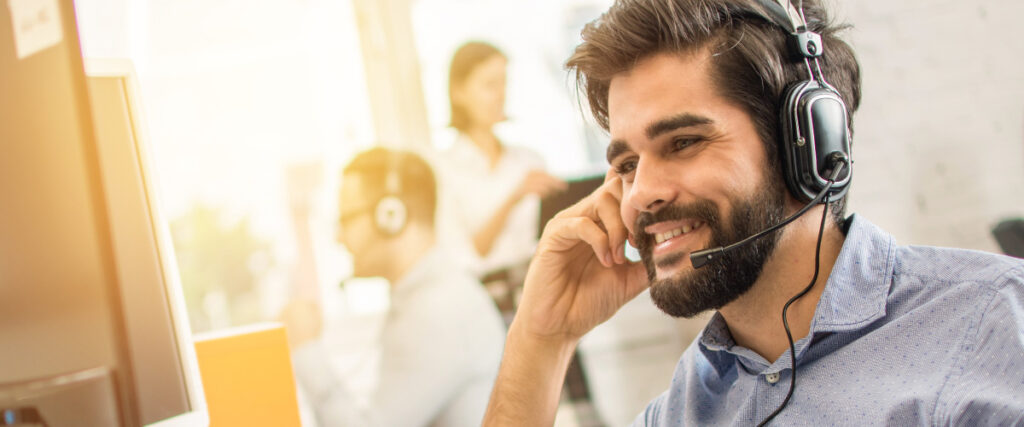
Talk with a Specialist
If you think it can’t be monitored, contact us, we might surprise you.
4. Enhanced Safety and Risk Management
Safety in industrial manufacturing is a paramount concern, and wireless power monitoring sensors significantly contribute to a safer working environment. These sensors provide immediate notifications about abnormal energy usage, which can be indicative of potential electrical hazards, system overloads, or equipment malfunctions.
This early warning system allows for prompt intervention, preventing accidents and reducing the risk of equipment damage or failure. In industries where electrical systems are critical, such as in heavy manufacturing, the ability to quickly identify and address electrical issues is vital for maintaining operational safety and preventing costly downtime.
Moreover, wireless sensors enhance safety by reducing the need for manual inspections in potentially hazardous areas. By remotely monitoring energy usage, the need for personnel to enter high-risk zones is minimized, thereby reducing exposure to potential safety hazards.
The data collected by these sensors also plays a crucial role in long-term risk management. By analyzing trends and patterns in energy usage, manufacturers can identify potential risks before they materialize, enabling a more proactive approach to safety and maintenance. This not only protects the workforce but also ensures the longevity and reliability of manufacturing equipment.
5. Data Integration and Smart Manufacturing
The integration of wireless sensors with other industrial Internet of Things (IoT) devices is ushering in a new era of smart manufacturing. These sensors serve as critical data points, contributing to larger systems that automate and optimize manufacturing processes. Their compatibility with existing IT infrastructures makes them an essential component of the smart factory ecosystem.
This integration facilitates advanced data analytics, allowing manufacturers to leverage big data for informed decision-making. By analyzing the vast amount of data collected from various sensors, manufacturers can gain insights into operational inefficiencies, predict maintenance needs, and optimize production schedules. This level of insight is crucial for staying competitive in an increasingly data-driven industry.
The integration of wireless power monitoring sensors with other systems enhances the overall functionality of the manufacturing process. For example, sensors can trigger automated responses to certain conditions, such as adjusting machine speeds or shutting down equipment in response to energy usage patterns. This level of automation not only improves efficiency but also ensures consistency and quality in production.
The ability of these sensors to seamlessly communicate with other devices and platforms is a cornerstone of Industry 4.0. It enables manufacturers to create interconnected, intelligent systems that can learn, adapt, and optimize themselves over time. As the manufacturing industry continues to evolve, the role of wireless power monitoring sensors in enabling these advanced capabilities will only become more significant.
6. Scalability and Flexibility
The dynamic nature of the manufacturing industry demands solutions that are not only effective but also scalable and flexible. Wireless power monitoring sensors meet these requirements by offering easy scalability and flexibility in deployment.
As manufacturing facilities grow or change their layout, wireless sensors can be easily added or repositioned to meet the new requirements. This scalability is a significant advantage over wired systems, which often require extensive and costly modifications to accommodate changes in the production environment.
Additionally, the flexibility of wireless sensors allows for customized deployment based on specific needs. For example, sensors can be deployed in specific areas of high energy use or in sections of the plant undergoing process changes. This tailored approach ensures that energy monitoring is always aligned with the most critical areas of the operation.
This flexibility also extends to the types of data that can be monitored and the ways in which it can be used. Beyond just monitoring power usage, these sensors can be configured to track a variety of parameters, such as temperature, humidity, and equipment performance. This versatility makes them a valuable tool for comprehensive operational monitoring and improvement.
The ability to integrate wireless sensors with other systems and platforms means that they can evolve alongside the broader technological landscape. As new technologies and standards emerge, wireless sensors can be updated or integrated with these advancements, ensuring that the manufacturing operation remains at the cutting edge of efficiency and innovation.
Remote Power Monitoring – A Must Have
The adoption of wireless power monitoring sensors in industrial manufacturing is a testament to the industry’s commitment to efficiency, cost-effectiveness, and sustainability. Swift Sensors continues to lead this transformation by providing innovative, reliable, and adaptable solutions. As the manufacturing world embraces these technologies, the potential for improved efficiency, reduced environmental impact, and enhanced competitiveness is immense. The future of industrial manufacturing is smart, connected, and sustainable, and wireless power monitoring sensors are a pivotal part of this exciting journey.
Stay in the Know with Swift Sensors
Sign up for the Swift Sensors newsletter to stay ahead in sensor technology. Get exclusive updates on industry trends, product releases, and special promotions. Elevate your knowledge and be part of our tech community. Signup now!