Wireless Sensors are the Future
In the dynamic world of industrial manufacturing, innovation is not just a luxury; it’s a necessity for survival and growth. Among the many technological advancements, the role of remote wireless sensors has been pivotal. Swift Sensors, a leader in this domain, is redefining traditional manufacturing paradigms. Remote wireless sensors are transforming how manufacturing processes are monitored, controlled, and optimized, leading to increased efficiency, productivity, and safety. This technology heralds a new era in manufacturing, where data-driven decisions are the norm, not the exception.
The Rise of Remote Wireless Sensors in Manufacturing
The evolution of remote wireless sensors in the industrial sector is a testament to the relentless pursuit of operational excellence. Traditional manufacturing relied heavily on manual monitoring and wired systems, which were often limited in scope and flexibility. The advent of wireless sensor technology marked a significant shift. These sensors, capable of collecting and transmitting data over wireless networks, offer real-time insights into various aspects of manufacturing processes. From monitoring equipment performance to environmental conditions, these sensors provide a level of oversight that was previously unattainable. This section will explore how wireless sensors evolved and their increasing adoption in the manufacturing sector.
Enhanced Efficiency and Productivity
A core benefit of remote wireless sensors is their ability to enhance efficiency and productivity. These devices provide continuous, real-time monitoring of critical parameters such as temperature, power, vibration, and humidity. With this data, manufacturers can swiftly identify and rectify inefficiencies, leading to improved production processes and product quality. This section can delve into specific case studies where wireless sensors have enabled manufacturers to achieve significant improvements, such as reduced waste, optimized production cycles, and improved quality control.
Cost Reduction and Energy Savings
In an industry where margins can be slim, cost reduction and energy savings are paramount. Remote wireless sensors play a crucial role in this aspect. By providing precise and timely data, these sensors help manufacturers optimize resource utilization, thereby reducing wastage and lowering energy consumption. This not only leads to cost savings but also contributes to environmental sustainability. This section can include real-world examples of how wireless sensors have been instrumental in saving costs for manufacturers across various sub-sectors, highlighting both financial and environmental benefits.
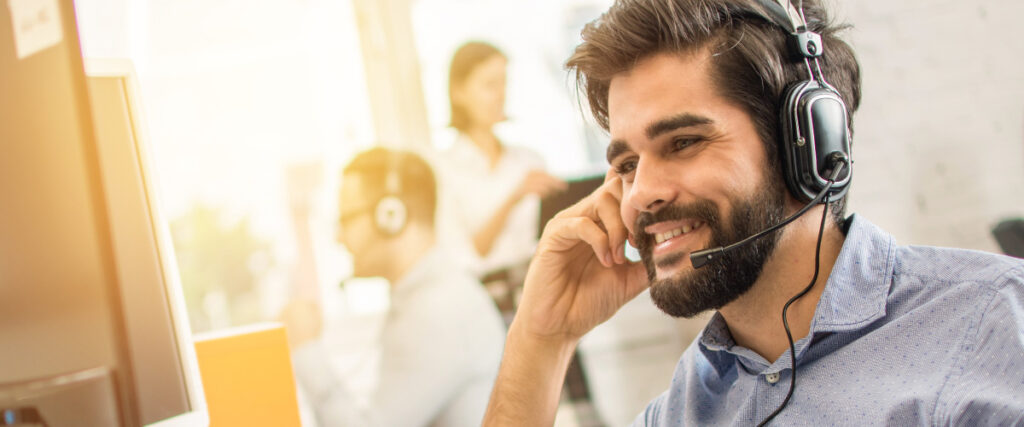
Talk with a Specialist
If you think it can’t be monitored, contact us, we might surprise you.
Predictive Maintenance and Downtime Reduction
Equipment failure and unplanned downtime can be costly for manufacturers. Remote wireless sensors offer a solution through predictive maintenance. By constantly monitoring equipment health, these sensors can predict failures before they occur, allowing for timely maintenance and repairs. This proactive approach significantly reduces downtime and extends the lifespan of equipment. This section can highlight the role of wireless sensors in predictive maintenance strategies, illustrating how they have helped manufacturers minimize downtime and maintenance costs.
Enhancing Worker Safety and Compliance
Manufacturing plants can be hazardous environments, making worker safety a top priority. Remote wireless sensors contribute significantly to creating safer workplaces. By continuously monitoring environmental conditions and machinery performance, these sensors can alert workers and management to potential hazards, preventing accidents and injuries. Furthermore, compliance with safety regulations and standards is a complex but crucial aspect of manufacturing. Wireless sensors simplify compliance by providing accurate, real-time data that can be used to demonstrate adherence to regulatory requirements. This section will discuss how wireless sensors contribute to workplace safety and regulatory compliance, using specific examples from various industries.
Integration with IoT and Smart Manufacturing
The integration of wireless sensors with the Internet of Things (IoT) and smart manufacturing systems represents a significant advancement in the manufacturing sector. This integration enables the creation of a fully connected, intelligent manufacturing environment. In such an environment, sensors not only collect data but also communicate with other devices and systems, automating various processes and decision-making. This section will explore how this integration is shaping the future of manufacturing, leading to more efficient, responsive, and adaptive manufacturing systems.
Bright Future
The revolution brought about by remote wireless sensors in industrial manufacturing is just beginning. Companies like Swift Sensors are at the forefront, pushing the boundaries of what’s possible in manufacturing efficiency, safety, and sustainability. As technology continues to evolve, the potential applications and benefits of wireless sensors in manufacturing will only grow, leading us into a new era of industrial innovation and productivity.
Stay in the Know with Swift Sensors
Sign up for the Swift Sensors newsletter to stay ahead in sensor technology. Get exclusive updates on industry trends, product releases, and special promotions. Elevate your knowledge and be part of our tech community. Signup now!