What Is Predictive Maintenance?
Predictive maintenance is a modern maintenance strategy that relies on the use of data and analytics to forecast when equipment is likely to fail or degrade in performance. Instead of waiting for something to break (reactive maintenance) or following a fixed schedule regardless of condition (preventive maintenance), predictive maintenance monitors equipment in real-time to detect early signs of potential issues. This approach allows maintenance teams to address problems before they lead to unexpected breakdowns, thereby reducing unplanned downtime and optimizing asset lifespans.
By leveraging predictive maintenance, manufacturers can drastically reduce operational interruptions, improve safety, and lower the total cost of ownership for machinery and infrastructure. This strategy is particularly beneficial in industries where even short periods of downtime can lead to significant financial losses or pose safety risks. The implementation of predictive maintenance is becoming more widespread thanks to advancements in sensor technology and connectivity, making it more accessible even to small and mid-sized manufacturing operations.
The Role of Wireless Sensors in Predictive Maintenance
Wireless sensors have emerged as a cornerstone technology in enabling predictive maintenance in manufacturing settings as well as many other applications. These sensors are compact, affordable, and easy to install, allowing for the seamless collection of real-time data from a wide range of industrial assets. Unlike traditional wired sensors, which can be expensive and time-consuming to deploy, wireless sensors can be placed on equipment with minimal disruption and without the need for extensive cabling or infrastructure modifications.
By continuously monitoring machinery for critical parameters like vibration, temperature, humidity, power consumption, and more, wireless sensors enable maintenance teams to maintain a constant watch over equipment health. The collected data is typically transmitted to cloud-based platforms or centralized dashboards, where it can be analyzed and acted upon. This always-on visibility allows teams to catch deviations from normal operating conditions early, providing a valuable head start in addressing maintenance issues before they escalate.
Continuous Equipment Monitoring
One of the most significant benefits of wireless sensors is their ability to provide continuous monitoring of key performance indicators for industrial machinery. These sensors can be strategically placed on motors, pumps, compressors, and other vital assets to track factors such as vibration patterns, operating temperatures, current draw, and environmental conditions. For example, a sudden increase in vibration could indicate bearing failure, while a rise in temperature may suggest overheating due to friction or electrical issues.
By detecting these anomalies in real-time, maintenance teams are empowered to intervene promptly—often before the issue becomes severe enough to cause downtime. This form of proactive oversight not only extends the life of the equipment but also ensures a safer working environment by minimizing the risk of catastrophic failures. Over time, this level of monitoring leads to a more stable and efficient production process, with fewer unexpected interruptions.
Simple, Scalable Deployment
Wireless sensors are incredibly versatile, making them an ideal choice for manufacturers looking to scale their predictive maintenance capabilities. Because these sensors are battery-powered and communicate wirelessly, they can be installed in locations that would otherwise be difficult, dangerous, or costly to reach with wired alternatives. This includes machinery located in remote parts of a facility, mobile assets, or equipment housed in environments with limited infrastructure.
The simplicity of installation also reduces the need for specialized labor, cutting down the overall cost of deployment. Additionally, manufacturers can begin with a small number of sensors and gradually expand their network as needs evolve, without major capital investment. This scalability is especially valuable in dynamic manufacturing environments where flexibility and speed are crucial to maintaining competitiveness.
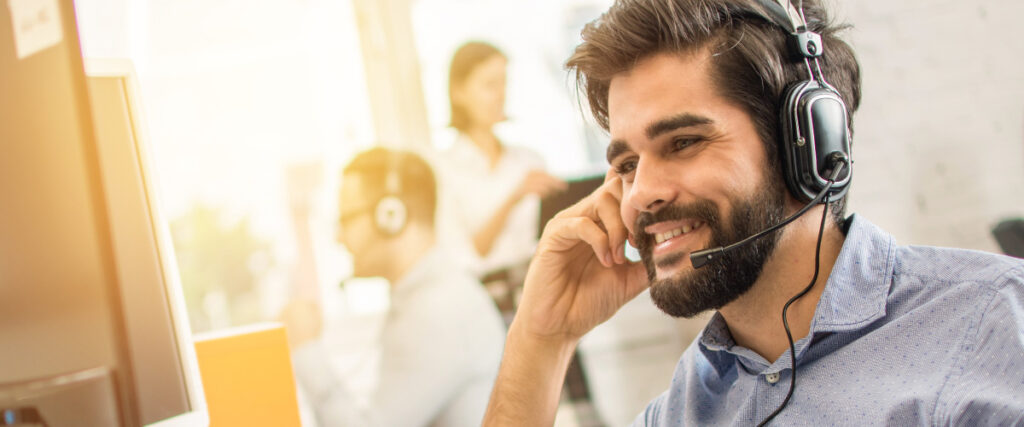
Talk with a Specialist
If you think it can’t be monitored, contact us, we might surprise you.
Alert-Based Proactive Maintenance
While some predictive maintenance systems rely on complex data modeling and AI algorithms, wireless sensors often provide value through a more straightforward method: threshold-based alerts. These alerts are triggered when sensor readings move outside of predefined ranges, such as a temperature exceeding safe limits or an unexpected spike in electrical current. These immediate, actionable notifications allow maintenance personnel to respond quickly and decisively.
This simplicity makes proactive maintenance accessible to facilities that may not yet have the resources to implement full-scale predictive analytics. Even with basic alerting, wireless sensors can significantly reduce downtime and repair costs by ensuring that potential issues are addressed before they cause operational disruptions. Over time, facilities can build on this foundation by integrating more advanced analytics, using historical data collected from the sensors.
Data-Driven Insights and Reporting
As wireless sensors collect data over time, they create a rich dataset that can be used for more than just immediate alerts. Maintenance teams can analyze historical trends to identify recurring issues, track the performance of individual machines, and optimize maintenance schedules based on actual usage and wear patterns. This data-driven approach enables smarter, more strategic decisions that go beyond gut instinct or traditional schedules.
For example, if a certain piece of equipment consistently shows early signs of wear during specific shifts or under certain load conditions, adjustments can be made to improve performance and longevity. Furthermore, these insights can support capital planning by providing evidence for machinery upgrades or replacements, ensuring that investments are made based on actual performance data rather than assumptions.
Real-World Applications in Manufacturing
In real-world manufacturing settings, the use of wireless sensors for predictive maintenance is delivering measurable benefits across a variety of applications. For instance, in CNC machining centers, vibration sensors can detect imbalances or misalignments in the spindle before they affect the accuracy of the cuts. In production lines, sensors monitoring motor temperature and current can identify overworked components that are at risk of failure, allowing maintenance teams to act preemptively.
Facilities that rely on refrigeration, such as food processors or pharmaceutical manufacturers, use temperature sensors to ensure compliance and protect valuable inventory. Even door sensors and open/close monitors play a role by tracking access to critical systems, improving both operational awareness and regulatory compliance. These examples illustrate the broad versatility of wireless sensors and their critical role in maintaining productivity and safety across manufacturing environments.
Smarter Maintenance Starts with Simpler Monitoring
Predictive maintenance is no longer a luxury reserved for high-tech facilities with massive IT budgets. With wireless sensors, even small and mid-sized manufacturers can implement an effective, scalable approach to proactive monitoring. These sensors provide a simple yet powerful way to identify potential equipment issues early, reduce unplanned downtime, and extend the life of machinery—all without requiring complex infrastructure or data science expertise.
Swift Sensors delivers wireless monitoring solutions that are easy to deploy, intuitive to use, and capable of transforming maintenance operations. By starting with simple, real-time monitoring and building toward more advanced analytics, manufacturers can create a maintenance strategy that grows with their needs, supporting long-term efficiency, safety, and profitability.
For more information on how Swift Sensors can help you, contact Swift Sensors today.
Stay in the Know with Swift Sensors
Sign up for the Swift Sensors newsletter to stay ahead in sensor technology. Get exclusive updates on industry trends, product releases, and special promotions. Elevate your knowledge and be part of our tech community. Signup now!